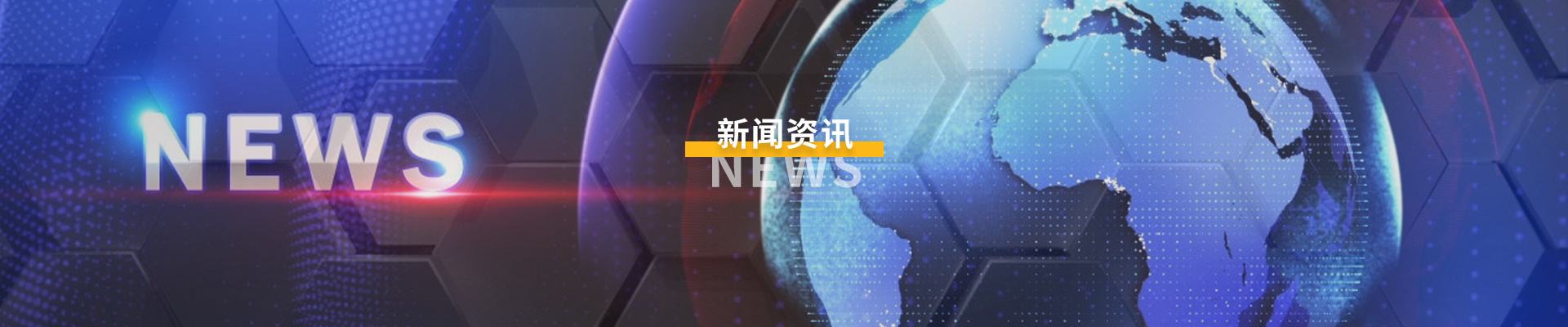
NEWS
CONTACT US
Shenzhen Mukun Trading Co., Ltd
Contact person:Mr. Dong Chengming
Tel:86 0755 89689959
Fax:86 0755 33620169
Postal code:518111
Address: No.107, Building M22, Hardware Chemical Plastic Zone, China South City Holdings, Pinghu Street, Longgang District, Shenzhen, Guangdong, China
Copper plating bath formula
Time:
2015-08-26 16:59
Source:
Formula 1 Copper Brush Plating Solution (Alkaline Copper)
Copper sulfate pentahydrate 250g/L; ethylenediamine 135g/L; add water to 1L
Process conditions: pH value 9.2-9.8, working voltage 8-14V, relative movement speed of anode and anode 6-12m/min, solution color is blue-purple, copper ion concentration 64g/L, power consumption coefficient 0.079A·h/(dm2 ·Μm), the safe thickness of the coating is 0.13mm, the coating volume is 716μm·dm2/L, and the coating hardness is HRC21. Add 2/3 of distilled water or deionized water to the container, and then add copper sulfate. After stirring to dissolve, slowly add ethylenediamine under constant stirring. After cooling to room temperature, adjust the pH to about 9.7 with sulfuric acid. Dilute with distilled water to the required volume.
Brush plating is mainly used to repair worn or processed out-of-tolerance parts. Improve the corrosion resistance of metal parts, increase the surface hardness, wear resistance, electrical conductivity and magnetic properties of the parts, and also improve the brazing properties of certain metals. It is also used in the finishing and protection of cultural relics and handicrafts. Before plating, cleaning, degreasing, rust removal, electric cleaning, activation and other processes are also required.
Recipe 2 bright copper plating (1)
Copper sulfate 150.0-250.0g/L; sulfuric acid 45.0-110.0g/L; zinc powder 0.5g/L; activated carbon 1.0-2.0g/L; appropriate amount of bright additives; water to 1.0L
Process conditions: temperature 20-50℃, cathode current density 1-3A/dm2.
Heat the copper sulfate with water to dissolve it, and slowly add sulfuric acid and the remainder of water under stirring after cooling. Add zinc powder and activated carbon for treatment, stir, filter, add additives and mix well before use. This product is simple in composition, stable in solution, and does not generate harmful gases during operation. With appropriate bright additives, bright copper coatings can be obtained with good leveling performance.
Recipe 3 bright copper plating (2)
Copper sulfate 200.0~250.0g/L; sulfuric acid 50.0~70.0g/L; glucose 30.0~40.0g/L; zinc powder 0.5g/L; activated carbon 1.0~2.0g/L; appropriate amount of bright additives; water to 1.0L
The production and use are the same as formula 2.
Recipe 4 bright copper plating (3)
Copper pyrophosphate 70.000~90.000g/L; Potassium pyrophosphate 300.000~380.000g/L; Ammonium citrate l0.000~15.000g/L; Selenium dioxide 0.008~0.020g/L; 2-mercaptobenzimidazole 0.002~ 0.004g/L; activated carbon 3.000~5.000g/L; hydrogen peroxide 1.000~2.000mL; appropriate amount of brightener; add water to 1.0L
Process conditions: pH value 8.0-8.8, temperature 30-50°C, current density 1-3A/dm2. The production and use are basically the same as formula 2. Only selenium dioxide is dissolved in water, and 2-mercaptobenzimidazole is dissolved in potassium hydroxide solution and added.
Recipe 5 bright copper plating (four)
Copper pyrophosphate 50.000-60.000g/L; Potassium pyrophosphate 350.000-400.000g/L; Ammonium hydroxide (25%) 2.000-3000mL; Selenium dioxide 0.008-0.020g/L; 2-mercaptobenzothiazole 0.002- 0.040g/L; activated carbon 3.000—5.000g/L; appropriate amount of brightener; add water to 1.0L
Process conditions: pH value 8.4-8.8, temperature 30-40°C, current density 0.5-1A/dm2. The production and use are the same as formula 2.
Recipe 6 citrate tartrate copper plating
Basic copper carbonate 55.000-60.000g/L; citric acid 250.000-280.000g/L; potassium tartrate 30.000-35.000g/L; sodium bicarbonate l0.000-15.000g/L; selenium dioxide 0.008-0.020g/L ; Antifungal agent 0.100—0.500g/L; add water to 1.000
Process conditions: pH value 8.5-10, temperature 30-40℃, current density 0.5-2.5A/dm2, cathode movement 25m/min, area ratio of cathode and anode is 1:1-1:1.5. Both citric acid and tartrate are good complexing agents for copper. Usually they are used in combination. They have a strong adsorption effect and activate the electrode surface. Copper can be plated directly on the surface of steel, and the coating is fine and smooth.
Formula 7 copper plating solution
Copper sulfate 80.000-120.000g/L; sulfuric acid (98%) 180.000-220.000g/L; additive (SH-110, siloxane-silicone series products) 0.005-0.020g/L; emulsifier (OP-21) 0.200—0.500g/L; chloride ions 0.020—0.120g/L; methyl violet 0.010g/L; add distilled water to 1.000L in the plating tank, slowly add concentrated sulfuric acid to the copper sulfate solution under stirring (if industrial For copper sulfate, it is necessary to add 1-2ml/L hydrogen peroxide and stir for about 0.5h, then add 3-5g/L activated carbon, stir for 1-2h and then stand overnight and then filter). Add methyl violet solution (or not), electrolysis with low current until the purple disappears; add SH-110 and emulsifier OP-21, add hydrochloric acid reagent at 0.1mL/L; dilute the above solution with distilled water to the point It can be used after the required volume.
Operating conditions: temperature 15-25℃, cathode current density 1-2.5A/dm2, stirring, cathode movement 14-20 times/min. When using compressed air to stir, the plating solution must be continuously filtered to prevent impurities in the plating solution from being brought into the plating layer; using the cathode to move can be filtered regularly.
Formulation 8 non-cyanide copper electroplating solution
Copper sulfate 100-200g; sulfuric acid 15-60g; add water to 1L
Formula 9 alkaline copper electroplating solution
90g copper pyrophosphate; 300g potassium pyrophosphate; 3mg ammonium hydroxide (28%); appropriate amount of gloss agent; add water to 1L
Formula 10 high-speed copper plating solution
Copper sulfate 1.4-1.6mol/L; sulfuric acid 0.5-0.7mol/L; add water to 1.0L
Process conditions: The flow rate of the plating solution is 2m/s, the temperature is 60-65°C, the current density can reach 250A/dm2, the deposition speed is 25-50μm/min, and the distance between the cathode and the anode is 3mm. Depositing copper on printed circuits has been practically used. If high-speed electroplating copper is used for copper clad wire, it not only saves copper, but also saves equipment and workshops. Compared with the general process, the cost is reduced by 20%-30%, so it has high economic value.
Formula 11 Electroless copper plating solution with high copper sinking rate and good stability
Copper sulfate 16g/L; Potassium sodium tartrate 15g/L; Disodium edetate 25g/L; Formaldehyde 15mL; Additive A[(stabilizer) 24mg/L; Additive B[(stabilizer) 20mg/L; water Add to 1L
Process conditions: pH value 12.8, temperature 38°C.
Process flow: removing copper foil epoxy resin board → degreasing → water washing → prepreg → activation → water washing → degumming → water washing v electroless copper plating.
The plating solution has good stability, and the copper sinking speed can reach 2.5~3.0μm/20min. The coating has good ductility and smooth appearance, and can be used for hole metallization of printed circuit boards and other plastic plating.
Formula 12 Copper Composite Plating (1)
Copper sulfate 120-210g/L; sulfuric acid 52-120g/L; particulate additive (a-Al203, particle size 0.3μn) 30g/L water to 1L
Process conditions: temperature 22℃, cathode current density 4A/dm2.
Dissolve copper sulfate in water, slowly add sulfuric acid to the water under stirring, and then mix the two solutions evenly. The particles are added to this formula after wetting treatment to form a composite plating solution for electroplating copper substrates. In addition to the properties of copper, the obtained coating also improves its hardness and wear resistance. The content of particles in the coating is 3%.
Recipe 13 Copper Composite Plating (2)
Copper sulfate 200g/L; sulfuric acid 52~120g/L; particulate additive (graphite powder, particle size 0.3μm) 100g/L; add water to 1L
Process conditions: temperature 20℃, cathode current density 5A/dm2. The content of particles in the coating is 6.1%. The production and use are the same as formula l2.
Recipe 14 Copper Composite Plating (3)
Copper sulfate 200g/L; sulfuric acid 50g/L; particulate additive (molybdenum disulfide, particle size 0.3μm) 100g/L
Process conditions: temperature 20℃, cathode current density 5A/dm2. The content of particles in the coating is 5.3%.
previous page